- TECHNOLOGIES & SOLUTIONS
- Technologies
- Solutions
WAREHOUSE MOBILE ROBOT
Warehouse mobile robots are defined as vehicles that can drive, accelerate and decelerate automatically without human intervention1. Compared with other conveying equipment, such as, conveyor belts, carousels, etc., warehouse mobile robots are not limited by terrain and space, thus they are flexible and efficient. The on-vehicle control system is the core of the warehouse mobile robot, and consists of a control panel, a computer console, a navigation system, a communication system and a driving machine. The car body system is the body of the warehouse mobile robot, including the chassis, the casing, the frame and other components. The movement system exists in a variety of forms, including front-wheel-drive three-wheel structure, two-wheel-drive, differential or independent steering four- or six-wheel structures. The transfer system used to perform tasks can be a raceway type, a forklift type or a mechanical type, etc. In order to avoid system failures and collisions, mobile robots are also equipped with safety aids, such as, obstacle detection, warning alarms, emergency stop and automatic charging.
1楊文華,「AGV專題|技術篇:AGV技術發展綜述」, 新戰略機器人網, 2015 年 12 月 14 日。
To ensure the accuracy of its travel path, the mobile robot needs a navigation system. According to the guided route, the navigation of the warehouse mobile robot can be divided into three types: fixed route, semi-fixed route and no fixed route. The specific principles involved, the pros and the cons of each are shown in Table 1.
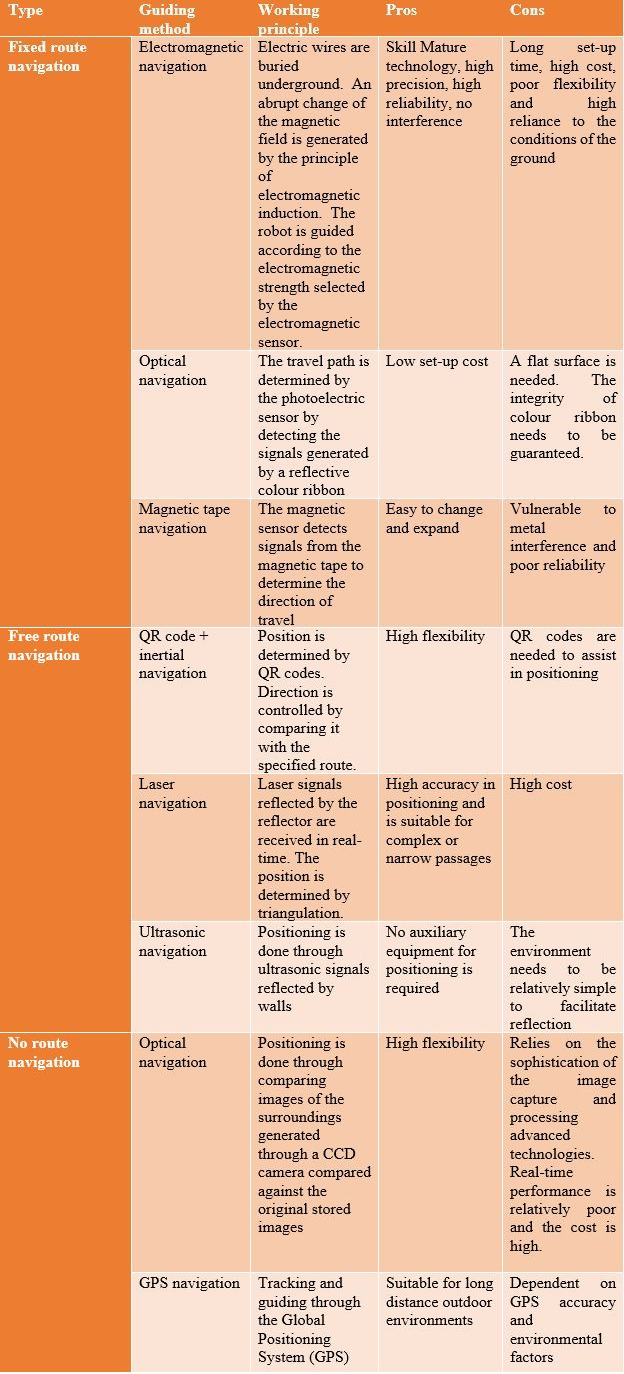