Introduction:
The Laboratory on Welding Technology and Simulation mainly focuses on the welding technology, quality control, and high-precision numerical simulations of the structural behaviour of welded sections for high strength S690 to S960 steel.
Research team:
Laboratory-in-charge
Prof. K. F. Chung
Members
Dr. M. F. Zhu (Deputy Laboratory-in-charge)
Dr. H. Jin (Deputy Laboratory-in-charge)
Mr. Y. C. Wang (Technical manager)
Mr. W. H Victor Wu (Project engineer)
Mr. S. H. Mike Mak (Project engineer)
Dr. Y. F. Hu (Research Assistant Professor)
Dr. K. Y. Ning (Postdoctoral Fellow)
Key research areas:
1. Welding technology for S690 to S960 high strength steel, and welding procedures specifications
2. Robotic welding for shop fabrication and site operation
3. Laser welding technology and quality
4. Mechanical properties of welded sections of thick steel plates
5. Heat affected zones and microstructural changes
6. Numerical simulations considering phase transformation
7. Inspection and quality assurance of welded sections
Research topics
Topic 1: Welding effect onto S690 thick steel sections
It is worth considering a pilot study reported by the authors that a number of butt-welded sections between 16 mm thick S690 steel plates were prepared using both gas metal arc welding (GMAW) and submerged arc welding (SAW) with different heat input energy q, i.e. q = 1.0, 1.5, 2.0 and 5.0 kJ/mm. Proportional cylindrical coupons with a diameter of 5 mm along their parallel lengths were tested, and the corresponding full range stress-strain curves are shown in Fig. 1. For those coupons extracted from the welded sections with q = 1.0, 1.5, 2.0 and 5.0 kJ/mm, it is found that
the reduction factors for their yield strengths are 0.98, 0.90, 0.86 and 0.70 respectively, and
the reduction factors for their tensile strengths are 1.00, 0.97, 0.92 and 0.83 respectively.
More importantly, for the two welded sections with q = 2.0 and 5.0 kJ/mm, their tensile strengths were found to be smaller than the required value of 770 N/mm2, as stipulated in EN ISO 15614. Hence, these two welded sections are rejected for structural application due to severe reductions in their mechanical properties after welding.
To facilitate the effective use of these high strength S690 steel in construction, a comprehensive investigation into the mechanical properties of 50 and 70 mm thick high strength S690 steel plates and their butt-welded connections under tension were conducted.
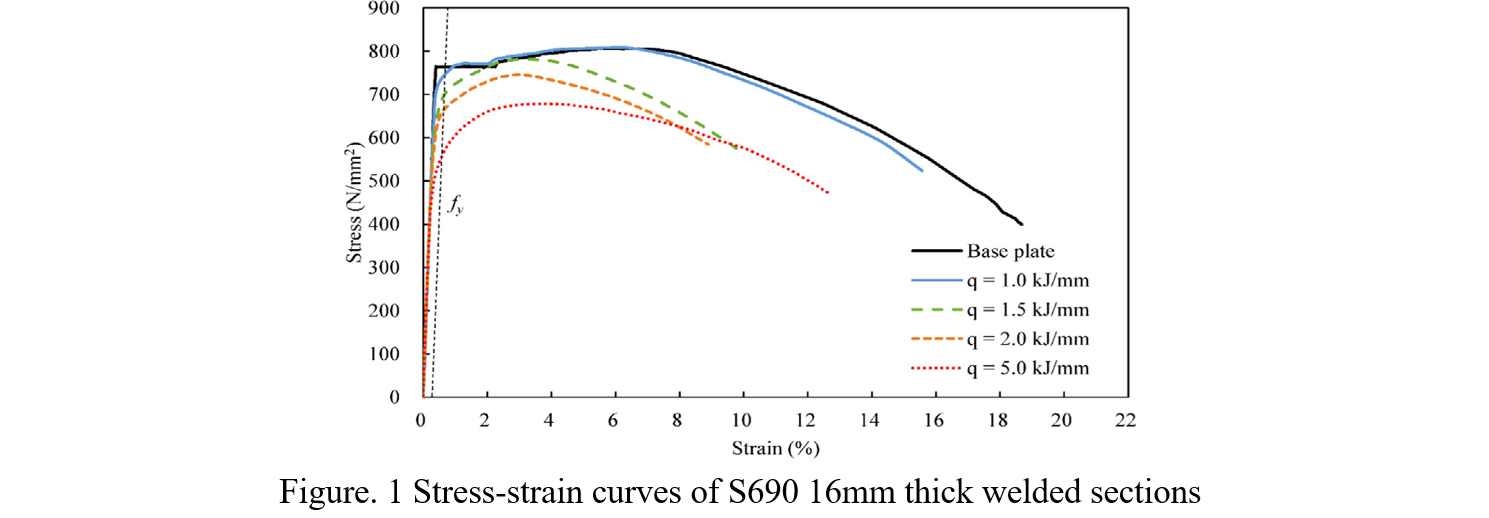
In typical fabrication of structural steel members, submerged arc welding (SAW) is often employed for welding thick steel plates in order to provide large heat input energy q to reduce the number of weld passes, A total of three butt-welded sections were fabricated with the 50 and 70 mm thick S690 QT steel plates using three different heat input energy q, i.e. 2.4, 3.5, and 5.0 kJ/mm, during welding. Standard tensile tests were then conducted, and the engineering stress-strain curves of these sections were shown in Fig. 2.
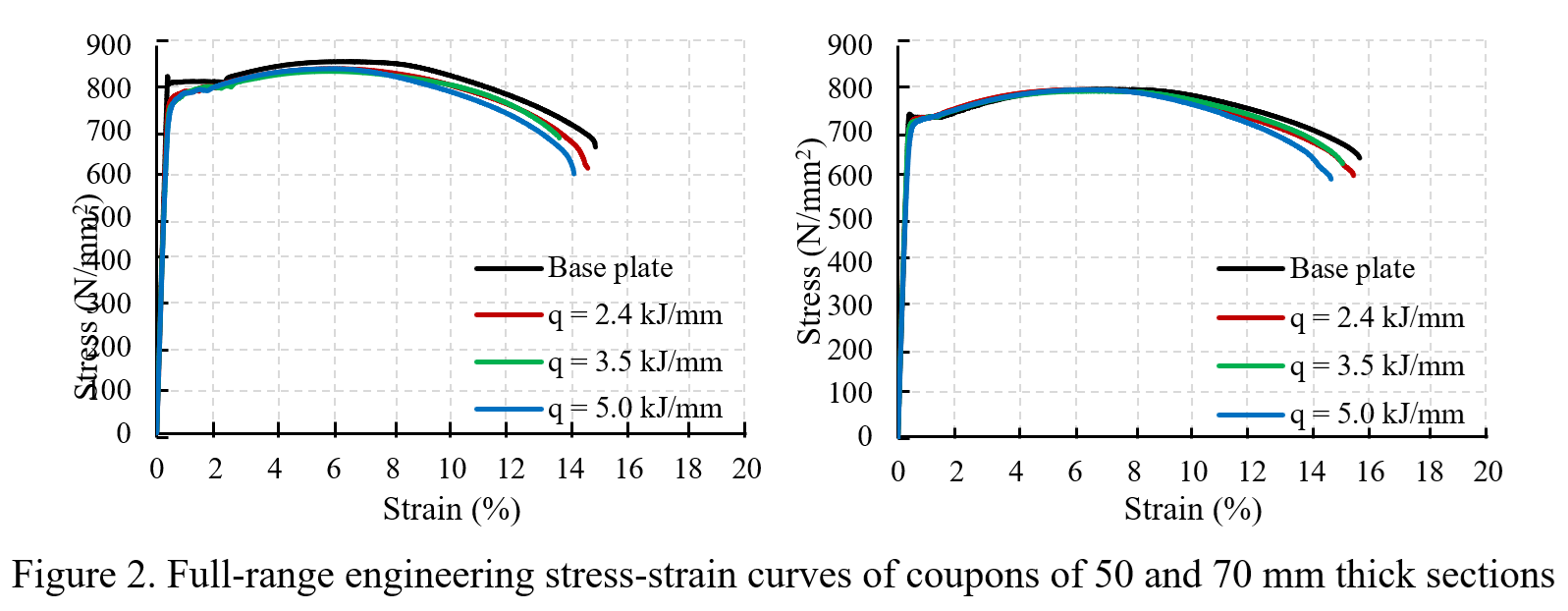
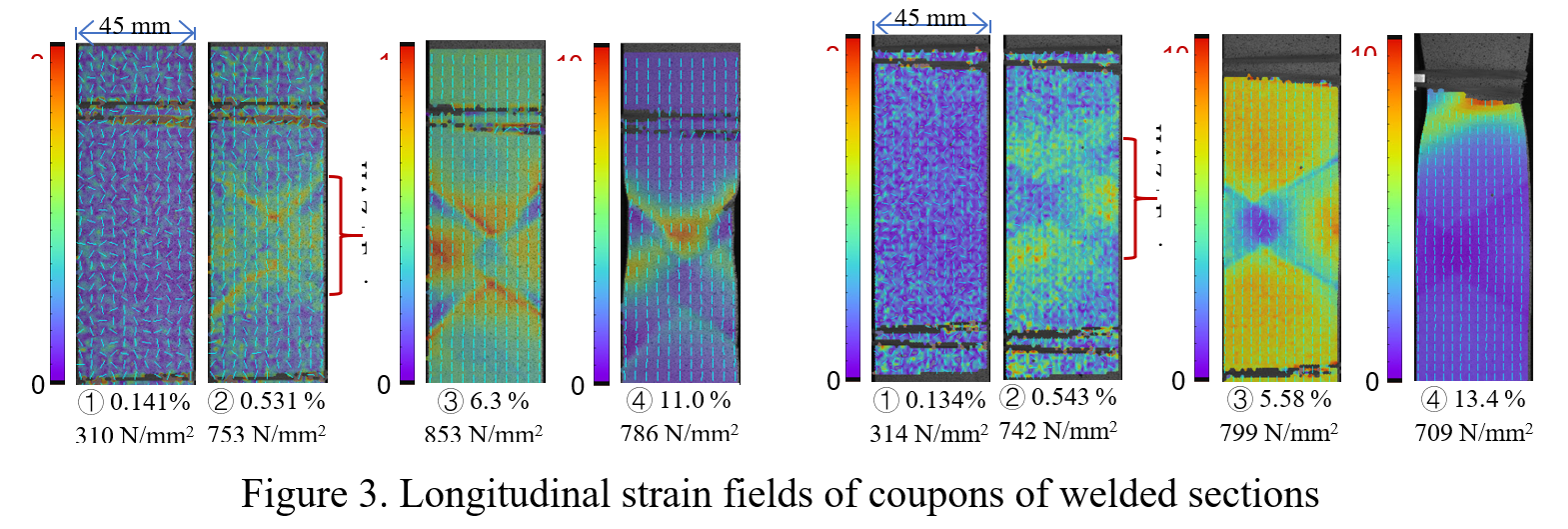
In general, it is considered to be important to control the heating as well as the cooling processes so that any microstructural change in the heat affected zones of the welded joints is kept to a minimum. This is generally achieved through a careful selection of various welding parameters according to geometrical details of the weld joints so that the heat input energy during welding is kept to a practical minimum, and yet, the welding process is performed with a high level of productivity. In order to facilitate a wide adoption of these high strength S690 steel in construction, it is important to investigate the effects of welding on the mechanical properties of these steel plates with practical thicknesses in construction, i.e. 30 to 80 mm thick. It is highly desirable to identify and quantify, if any, reductions in various mechanical properties of these welded sections, and more importantly, to eliminate any such reduction in these welded sections.
Topic 2: Advanced numerical simulation on high strength steel welding
During the past fifty years, a large number of experimental investigations were carried out to examine residual stresses and structural performance in fabricated structural members of S235 and S355 steels. However, the specialized quenching and tempering (QT) process applied on the high strength steel during smelting process enhances their strength to meet the demanding requirements of high levels, as well as good ductility and weldability. The QT process introduces complexities in the microstructure of the steel, and variations in cooling rates during welding can impact the resulting metal phases. In-depth research into these phase transformations during the welding of S690 and S960, both experimental and numerical, is essential for optimizing welding processes, ensuring the structural integrity of welded joints, and maximizing the benefits of high strength steel in engineering applications.
To investigate the solid phase transformations occurring in S960 during heating and cooling stages, it is necessary to obtain its continuous cooling transformation (CCT) curve. After getting the CCT curves from dilatometry test, four S960 welded sections with different cross-sectional thicknesses were fabricated, and temperature tests during welding as well as residual stress tests post-welding were performed, to provide effective calibration data for numerical simulations.
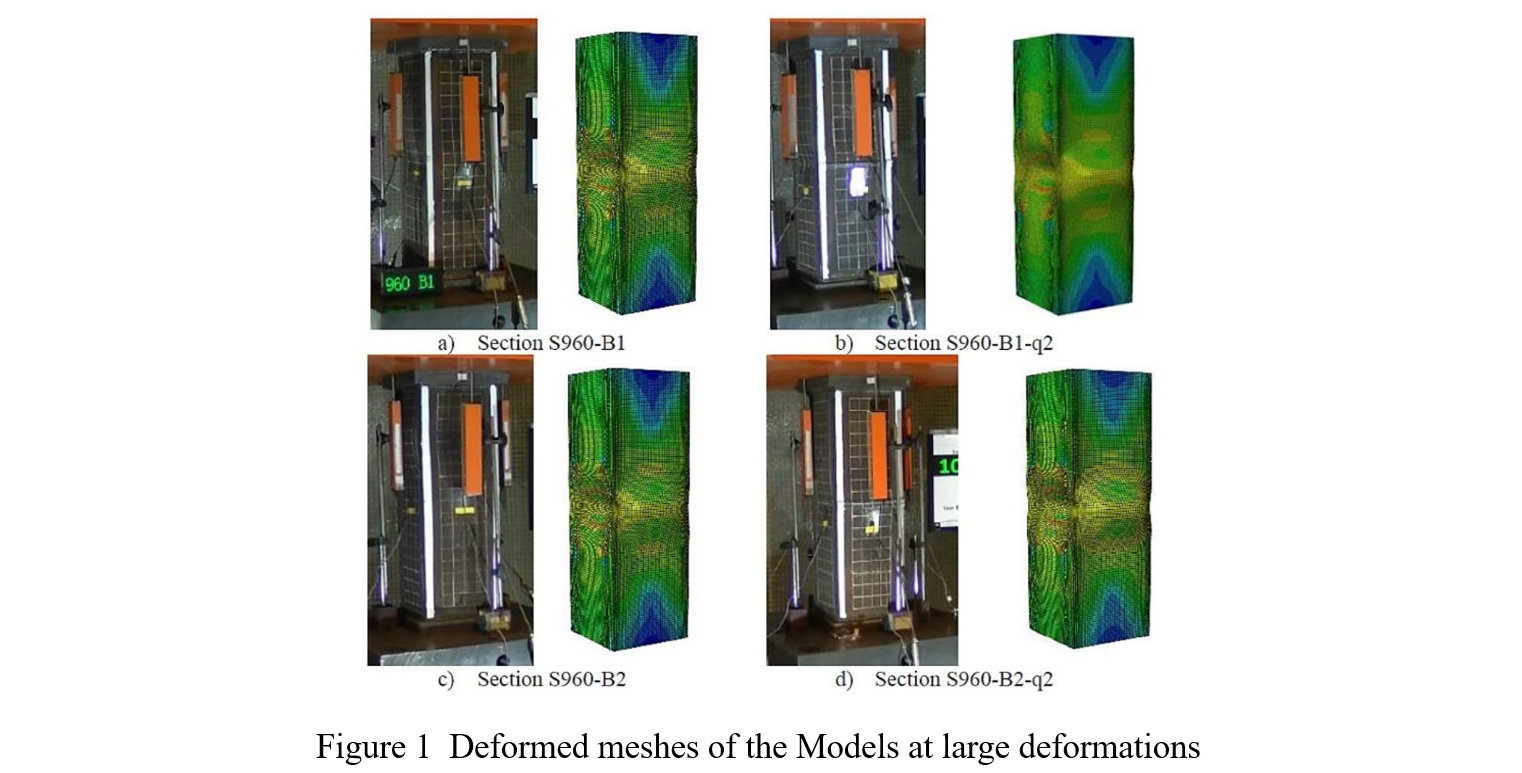
To investigate the structural behaviour of the S690 and S960 welded stocky columns under axial compression, a series of compression tests were performed in the Structural Engineering Research Laboratory of the Hong Kong Polytechnic University, as shown in Figure 1.
Numerical investigation
Figure 2 illustrates the complete process of the TMMS simulation approach. This method, which considers solid-state phase transformations during the welding process, encompasses analyses in heat transfer, thermo-metallurgy, thermo-mechanics, and structural performance. By employing Python scripts to connect the two finite element simulation software together, it provides specific information on the solid phase changes and mechanical property variations of high strength steel S960 in welded sections and heat-affected zones.
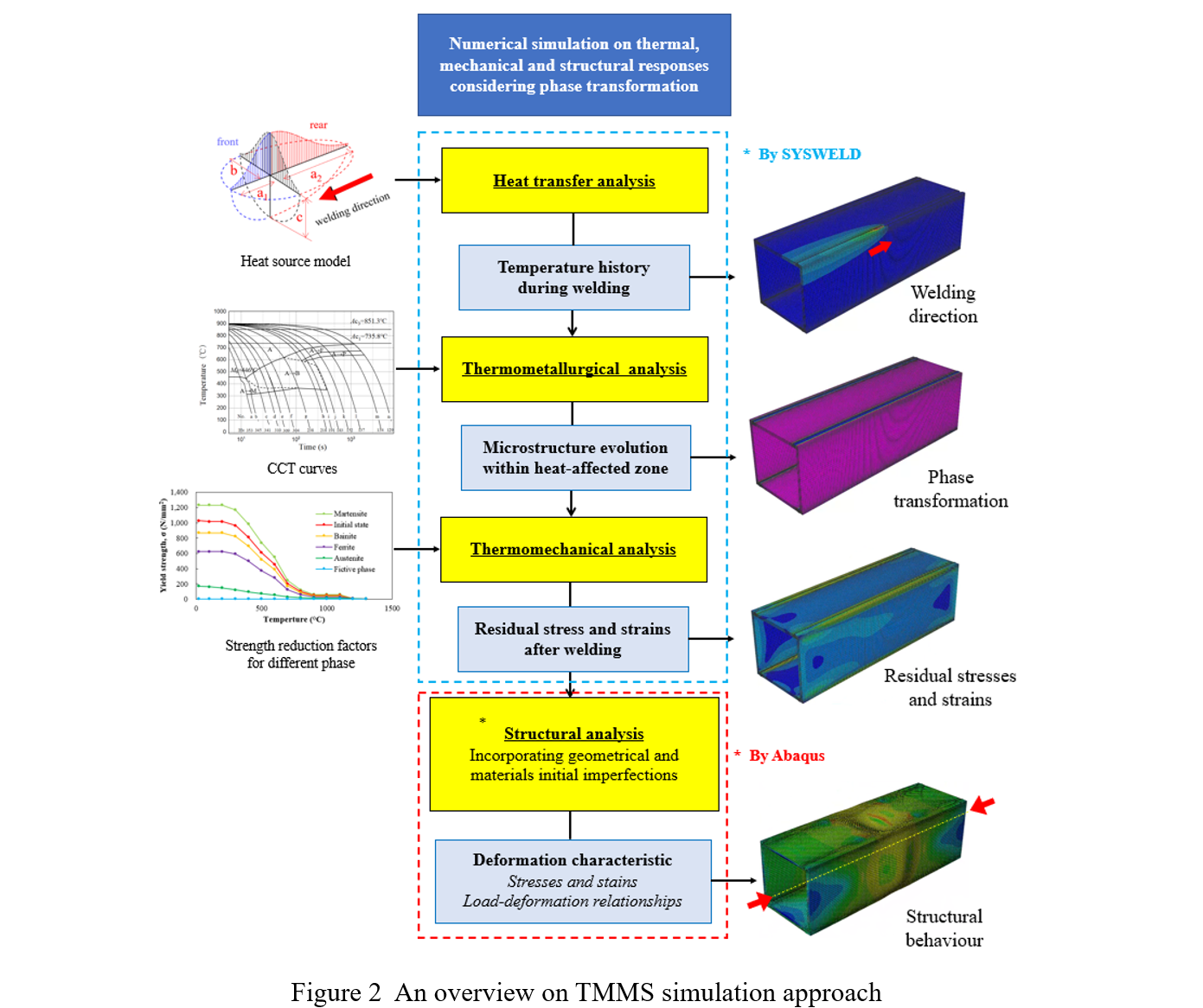
Finite element models of these steel plates with uniform metallurgical properties (homogeneous microstructures) are transformed under a direct exposure to transient temperature distribution history according to the maximum temperatures and the amount of heat input energy experienced during welding, and good comparisons among the predicted and the measured deformation characteristics of these columns over the entire deformation ranges were successfully achieved.
Topic 3: Mechanical behaviour and microstructure of high strength S690 steel laser-arc hybrid welded sections
Current research on laser-arc hybrid welding (LAHW) applications in steel structures encompasses diverse steel grades, including high strength and ultra high strength steel. However, existing studies on high strength and ultra high strength steel primarily focus on joint configurations and effects of weld metal chemistry on mechanical properties. A significant knowledge gap persists regarding the mechanical behaviour and microstructure of the welded joints of high strength S690 steel prepared with a LAHW, particularly under varying heat inputs. Understanding the impact of heat input energy on weld quality is critical for optimizing welding parameters and ensuring structural integrity. This study aims to fill this research gap by experimentally investigating the mechanical behaviour and microstructure of the welded sections of high strength S690 steel prepared with LAHW.
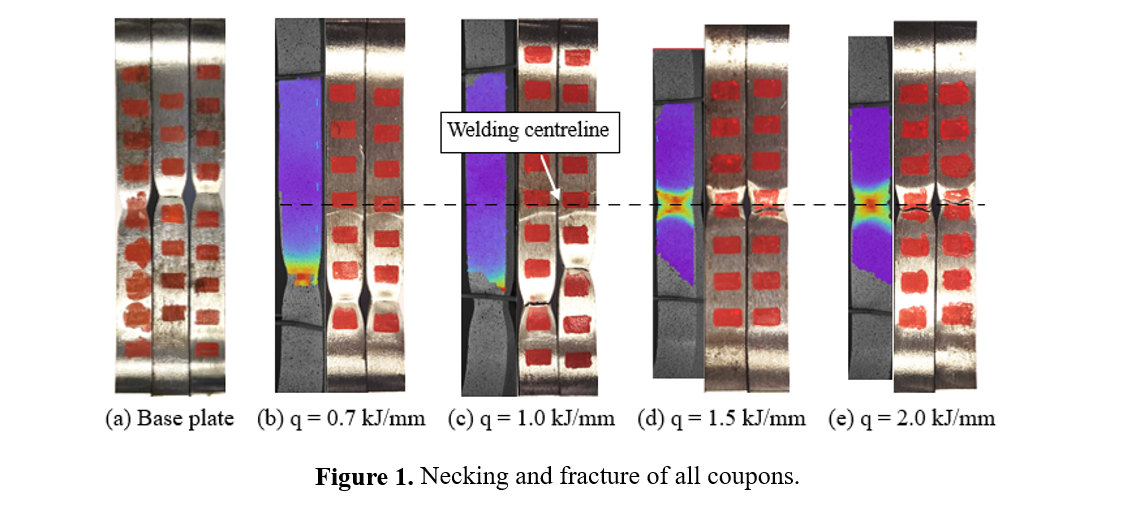
Experimental results reveal that heat input energy affects critically both tensile strength and failure modes of these welded sections. For those welded sections with low heat input energy (≤1.0 kJ/mm), the welded sections were found to be able to retain at least 98 % of the strengths of the base plates. For those welded sections with high heat input energy (≥1.5 kJ/mm), there is a notable degradation in strength. A reduction up to 24% in their yield strengths is found for those welded sections with a heat input energy at 2.0 kJ/mm, and fracture is found to take place in the fusion zones of the welded sections. It is also shown that with the help of digital image correlation, excessive heat input energy may cause softening in their fusion zones, compromising structural integrity.
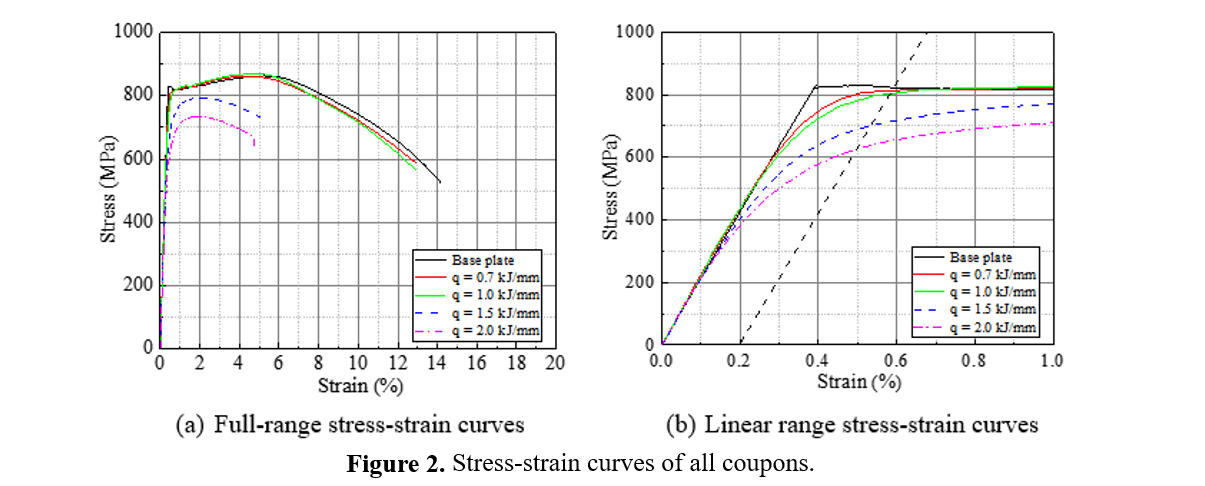
The microstructure analysis of the welded sections reveals distinct characteristics influenced by heat input levels. At low heat input energy , the fusion zone (FZ) primarily consists of martensite, particularly in the top region, resulting in high hardness. In contrast, at high heat input energy, the microstructure becomes predominantly bainite across the FZ, leading to a reduction in overall strength and hardness. This transition from martensite to bainite in the FZ at high heat input energy directly correlates with the degradation of tensile strength and localized fractures within the FZ.
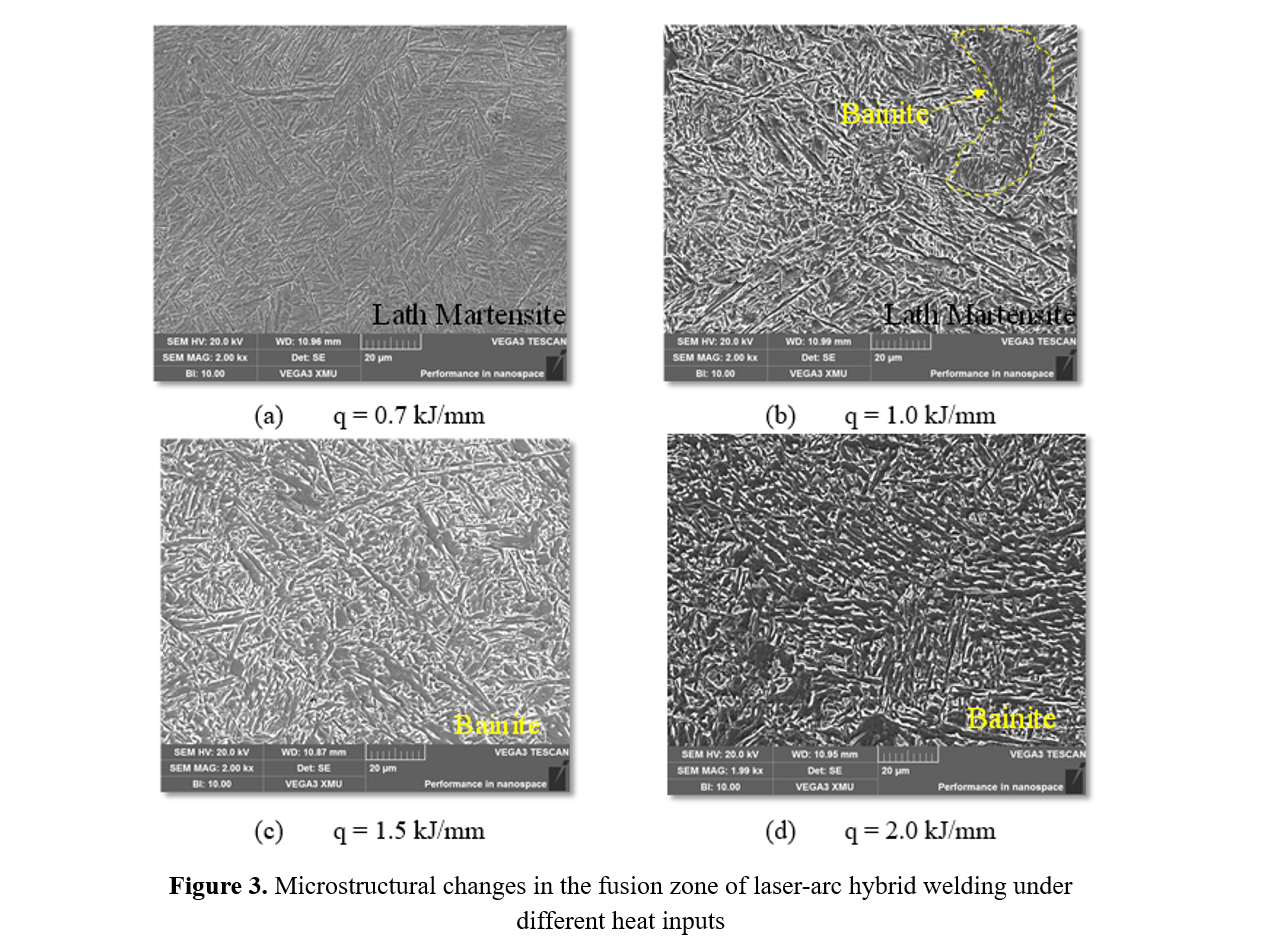
Representative papers
1. Liu, X., Chung, K. F., Ho, H. C., Xiao, M., Hou, Z. X., & Nethercot, D. A. (2018). Mechanical behavior of high strength S690-QT steel welded sections with various heat input energy. Engineering Structures, 175, 245-256.
2. Hu, Y. F., Chung, K. F., Ban, H., & Nethercot, D. A. (2020). Investigations into residual stresses in S690 cold-formed circular hollow sections due to transverse bending and longitudinal welding. Engineering Structures, 219, 110911.
3. Hu, Y. F., Ho, H. C., Chung, K. F., Xiao, M., Liu, X., & Nethercot, D. A. (2023). Integrated and coordinated numerical simulations on fabrication processes of high strength S690 cold-formed circular hollow sections. Engineering Structures, 279, 115620.
4. Xiao, M., Hu, Y. F., Chung, K. F., & Nethercot, D. A. (2024). Advanced numerical simulations on S690 cold-formed square hollow sections under compression. Journal of Constructional Steel Research, 212, 108303.
5. Jin, H., Zhu, M. F., Hu, Y. F., Ho, H. C., Chung, K. F., Nethercot, D. A., ... & Xie, G. (2024). Investigations into mechanical properties of 50 and 70 mm thick high strength S690 butt-welded sections. Engineering Structures, 314, 118363.
6. Zhu, M. F., Hu, Y. F., Han, Y. W., Chung, K. F., & Nethercot, D. A. (2025). Numerical investigation into high-strength S690 and S960 stocky welded H-sections under compression. Journal of Constructional Steel Research, 228, 109455.
7. Jin, H., Zhu, M. F., Wang, Y. C, Hu, Y. F, Ho, H. C., Chung, K. F., ... & Xie, G. Investigation into Mechanical Properties of Heat-Affected Zones in High Strength S690 Steel Welded Sections. Available at SSRN 4951420.
8. Zhu, M. F., Chung, K. F., Hu, Y. F., Jin, H., Han, Y. W., & Huang, M. X. (2025). Advanced numerical simulation on effects of welding onto high strength S690 and S960 steel welded H-sections. Engineering Structures, 323, 119236.
9. Zhu, M. F., Chung, K. F., Hu, Y. F., Jin, H., Xiao, T. Y., & Huang, M. X. (2025). Numerical simulation considering phase transformations on stocky columns of high strength S960 steel welded box sections under compression. Engineering Structures, 332, 120095.
10. Jin, H., Zhu, M. F., Advanced numerical simulation on high strength steel with welding-induced reductions in their mechanical properties. (Submitted)